Written by Allen Buckley in 1995 for Cornwall Today Magazine
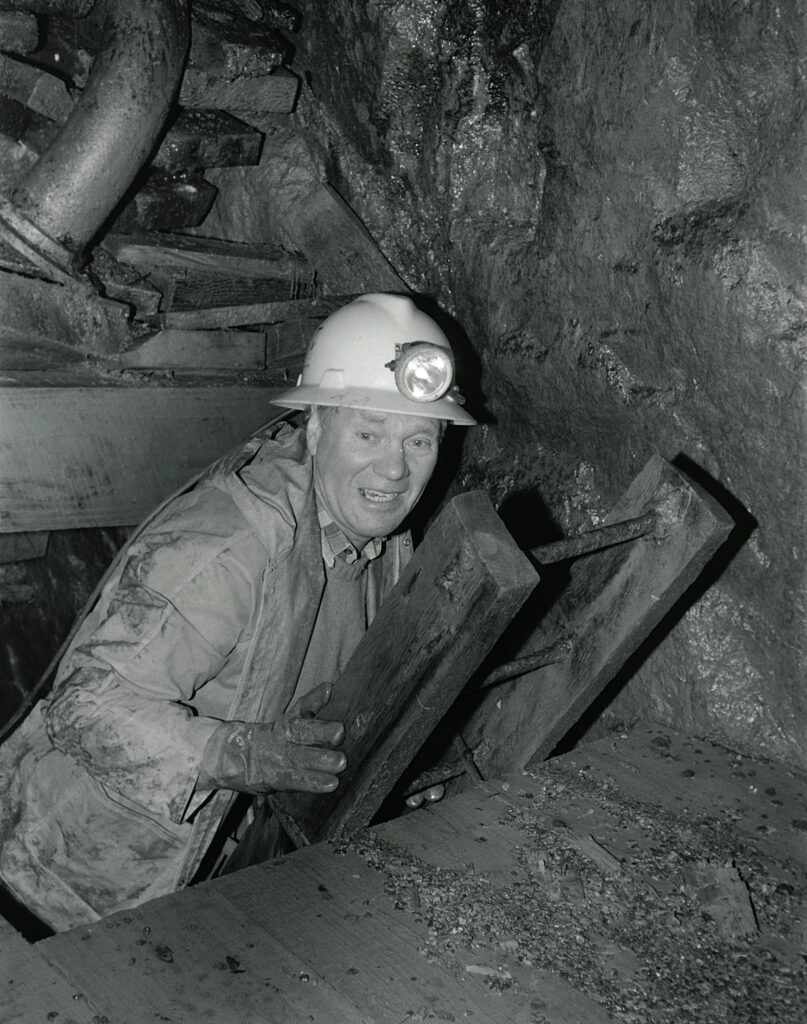
Over the last five hundred years Cornish miners have swung between being world leaders in mining methods and technology and being obsolescent and totally outdated in attitude and equipment.
During the 16th century Cornwall held its own; during the 17th century her miners and engineers began to take the lead, and during the 18th and early 19th centuries the Cornish dominated the world in most aspects of mining.
An area where the Cornish first lagged behind and then quickly caught up and returned to centre stage, was in the use of compressed-air powered rock drills. From the introduction of gunpowder shot-hole blasting into Cornish mines, in the late 17th century, holes had been drilled by “hand labour”. Three men working together in a typical underhand stope could expect to drill two four foot holes in a shift.
This began to change in the 1860s when F. B. Doering introduced a compressed-air rock drilling machine into mining. One was tried at Dolcoath with some success. It was the involvement of two Cornishmen in Barrow-in-Furness, ‘Lancashire, that first produced a successful machine into Cornish mines.
The Barrow Rock Drill, experimented with at Dolcoath and introduced at South Crofty in 1876, convinced the Cornish that here was a machine which would transform mining. This reciprocating machine was made of gunmetal and weighed 1201b., Mounted on a bar-and-arm it could be easily manoeuvred to drill holes at various angles. It worked fairly efficiently with air compressed to 50 psi.. The Barrow was quickly followed by other Cornish machines, with R. Stephens & Son at Pool, Holman Brothers at Camborne, Tuckingmill Foundry and Sara’s Foundry at Redruth, all producing machines of varying quality. Soon Stephens and Holman were exporting their “drifters”, some weighing up to 3001b.. all over the world.
By 1914, a great variety of Cornish and foreign rock drills were available, including light-weight, peg-leg stopers. Most of these machines by then had a “water line” which carried water through the drill steel to the toe of the hole, damping down dust and rendering the operation more efficient and far healthier.
South Crofty and some other Cornish mines continued to use ”hand labour” in stapes until long after the availability of the light-weight stopers. By the end of the 1920s, Stephens (now known as Climax) and Holmans were producing extremely fine machines with speed, economy and efficiency improving constantly.
During the 1940s and 1950s improved air-pressure through better compressors, the introduction of the tungston-carbide bit and the invention and development of the manoeuvrable air-leg, in all of which Cornish engineers played their part, gradually transformed mining in Cornwall as it did elsewhere. Coincidental with the introduction of powered rock drills was the invention and first use in Cornwall of high explosives – especially dynamite. From the 1870s dynamite had proved safe, efficient and effective, and despite the questionable use of the dynamite patent to keep costs artificially high, its use was very economical. South Crofty has routinely used ANFO (Ammonium Nitrate Fuel Oil) explosives for some years now, and from the costs standpoint this is certainly a major factor in the mine’s survival.
Cornish mining in 1995 was once again struggling to cope with low tin metal prices and high operating costs. As in the past South Crofty Mine has had to balance the expense of introducing new technology with the undoubted benefits of the enhanced pro-duction created by such investment.
Within these economic constraints Cornish miners have the use of some of the best rock drills and ore loading equipment available. As always it is the skill and enthusiasm of the miners themselves which can prove the decisive factor in the ultimate success and survival of Cornish Mining.
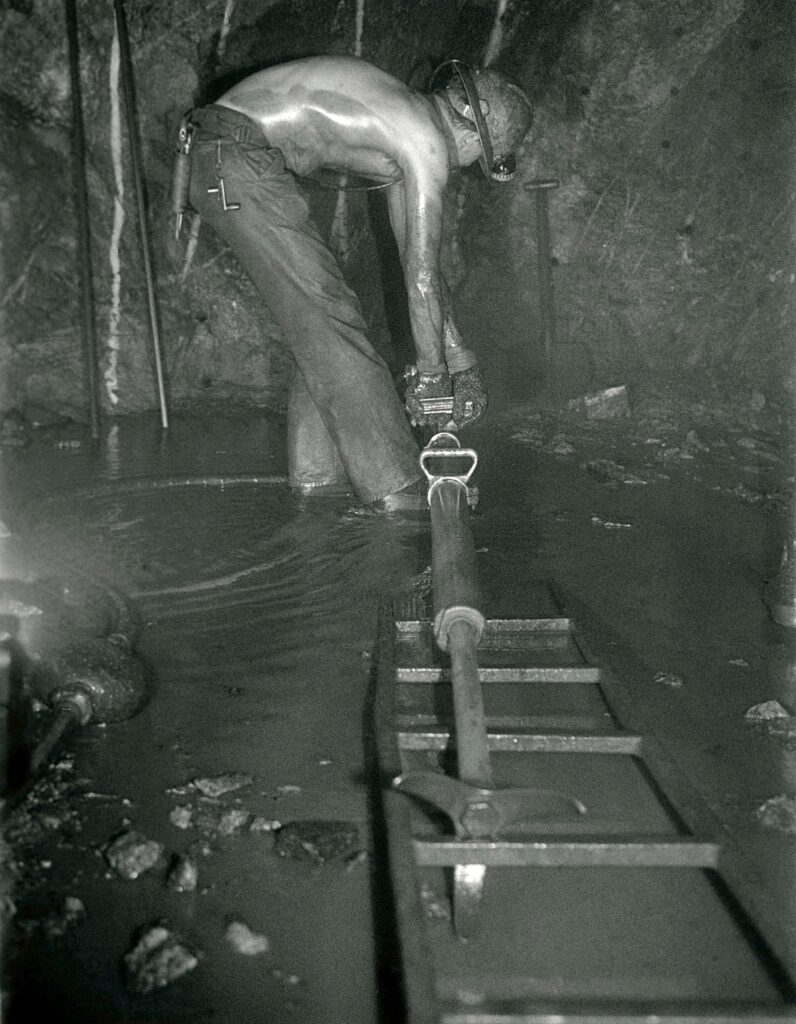
Thanks to Simon Jones for taking and letting us use his photos. Have a look at his brilliant site.
There are many many wonderful photos and well worth a visit. www.cornishmineimages.co.uk